高铁牵引变压器用绝缘加工件,需在高频交变磁场中保持低损耗,采用纳米晶合金与绝缘薄膜复合结构。通过真空蒸镀工艺在 0.02mm 厚纳米晶带材表面沉积 1μm 厚聚酰亚胺薄膜,层间粘结强度≥15N/cm,磁导率波动≤3%。加工时运用精密冲裁技术制作阶梯式叠片结构,叠片间隙控制在 5μm 以内,配合真空浸漆工艺(粘度 20s/25℃)填充气隙,使整体损耗在 10kHz、1.5T 工况下≤0.5W/kg。成品在 - 40℃~125℃温度范围内,磁致伸缩系数≤10×10⁻⁶,且局部放电量≤0.5pC,满足高铁牵引系统高可靠性、低噪音的运行要求。注塑加工件的分型面经精密研磨,合模线细至 0.1mm,不影响外观。绝缘加工件生产厂家
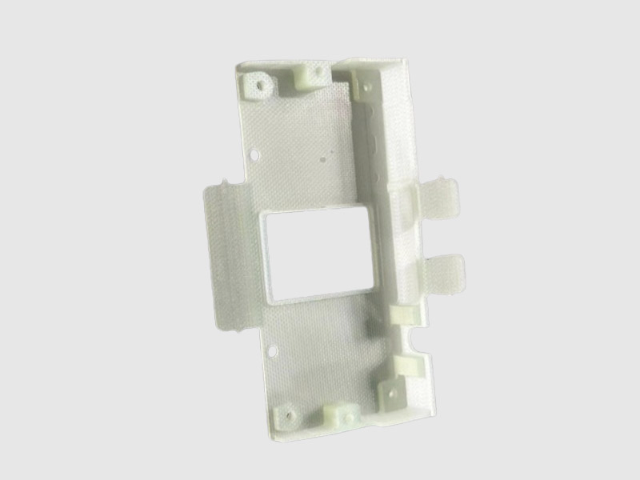
石油勘探井下的绝缘加工件,需抵抗超高压与强酸碱腐蚀,选用聚醚砜(PES)与碳化钨颗粒复合注塑成型。在原料中添加 30% 碳化钨(粒径 5μm),通过双螺杆挤出机(温度 360℃,转速 300rpm)实现均匀分散,制得抗压强度≥200MPa 的绝缘件。加工时采用高压注塑工艺(注射压力 180MPa),使制品孔隙率≤0.05%,配合电火花加工制作深径比 10:1 的密封槽,槽底圆角半径≤0.1mm。成品在 150℃、150MPa 井下压力环境中,耐 20% 盐酸溶液腐蚀 1000 小时后,质量损失率≤0.5%,且绝缘电阻≥10¹²Ω,确保随钻测井仪器在复杂工况下的信号传输稳定。防腐蚀加工件报价绝缘加工件的边缘经过倒角处理,避免划伤导线,提升设备安全性。
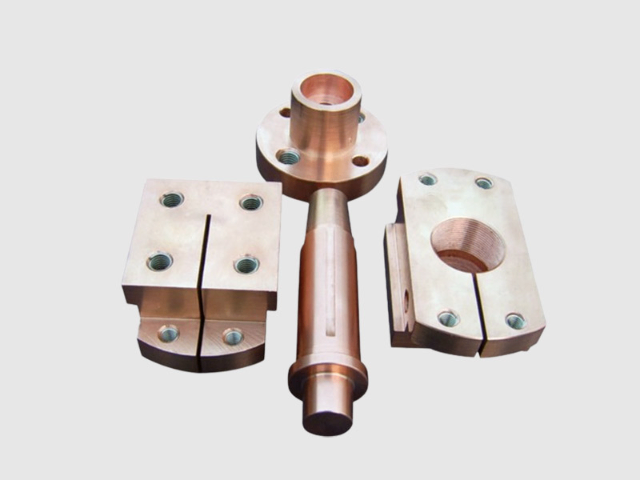
5G 基站用低损耗绝缘加工件,采用微波介质陶瓷(MgTiO₃)经流延成型工艺制备。将陶瓷粉体(粒径≤1μm)与有机载体混合流延成 0.1mm 厚生瓷片,经 900℃烧结后介电常数稳定在 20±0.5,介质损耗 tanδ≤0.0003(10GHz)。加工时通过精密冲孔技术(孔径精度 ±5μm)制作三维多层电路基板,层间对位误差≤10μm,再经低温共烧(LTCC)工艺实现金属化通孔互联,通孔电阻≤5mΩ。成品在 5G 毫米波频段(28GHz)下,信号传输损耗≤0.5dB/cm,且热膨胀系数与铜箔匹配(6×10⁻⁶/℃),满足基站天线阵列的高密度集成与低损耗需求。
轨道交通用绝缘加工件对防火性能要求极高,以环氧树脂玻璃布层压板为例,需通过 EN 45545 - 2 标准的 R22 级测试,燃烧时热释放速率峰值≤300kW/m²,烟毒性等级达 SR2。加工过程中采用数控铣削配合低温冷却(-20℃)技术,避免切削热导致材料碳化,加工后的触头盒绝缘件需进行真空干燥处理,含水率控制在 0.5% 以下。成品在 150℃热老化 1000 小时后,弯曲强度保留率≥80%,且在交变湿热环境(40℃,93% RH)中测试 72 小时,绝缘电阻仍≥10¹²Ω,满足高铁牵引变流器的严苛工况需求。绝缘加工件的孔径与槽位经数控加工,配合精度高,安装便捷高效。
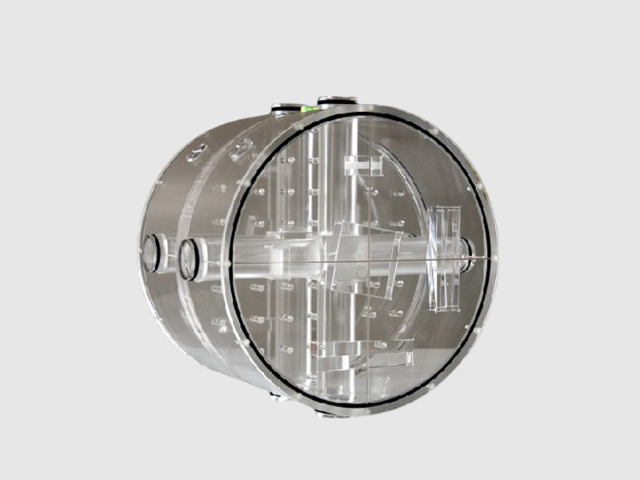
新能源汽车电驱系统注塑加工件选用改性 PA66+30% 玻纤与硅烷偶联剂复合体系,通过双阶注塑工艺成型。一段注射压力 160MPa 成型骨架结构,第二段保压 80MPa 注入导热填料(Al₂O₃粒径 2μm),使材料热导率达 1.8W/(m・K)。加工时在电机端盖设计螺旋式散热槽(槽深 3mm,螺距 10mm),配合模内冷却(冷却液温度 15℃)控制翘曲量≤0.1mm/m。成品经 150℃热油浸泡 1000 小时后,拉伸强度保留率≥85%,且在 100Hz 高频振动(振幅 ±0.5mm)测试中运行 5000 小时无裂纹,同时通过 IP6K9K 防护测试,满足电驱系统的散热、耐油与密封需求。防静电注塑件添加碳纤填料,表面电阻控制在 10⁶-10⁹Ω 区间。防腐蚀加工件报价
精密加工的绝缘件具有良好的机械强度,能承受设备运行中的振动与冲击。绝缘加工件生产厂家
在高频电子设备中,绝缘加工件的介电性能至关重要,聚四氟乙烯(PTFE)加工件凭借≤2.1 的介电常数和≤0.0002 的介质损耗,成为微波器件的较好选择材料。加工时需采用冷压烧结工艺,将粉末在 30MPa 压力下预成型,再经 380℃高温烧结成整体,避免传统注塑工艺产生的内应力。制成的绝缘子在 10GHz 频率下,信号传输损耗≤0.1dB/cm,且具有 - 190℃至 260℃的宽温适应性,即便在极寒的卫星通讯设备或高温的雷达发射机中,也能保证电磁波的无失真传输。绝缘加工件生产厂家
文章来源地址: http://dgdq.ehsy.com-m.chanpin818.com/lianjieqi/qtljq/deta_29047053.html
免责声明: 本页面所展现的信息及其他相关推荐信息,均来源于其对应的用户,本网对此不承担任何保证责任。如涉及作品内容、 版权和其他问题,请及时与本网联系,我们将核实后进行删除,本网站对此声明具有最终解释权。